SERVICES
Service Process
conversation
Start with us a conversation
solution
Customized your production line
quote
Send an estimation & confirm the contract
scheduling
Arrange your machine for production
delivery
The solution is delivered in time
repair
Lifetime after-sales service
Production Quality Management
As a manufacturer of aluminum door and window production equipment certified by ISO9001, JH adheres to strict and standardized quality management practices to ensure that each product achieves the highest level of excellence. By aligning our processes with ISO9001 standards, we ensure the quality and safety of our equipment and showcase our commitment to delivering outstanding service and support to our worldwide clients.
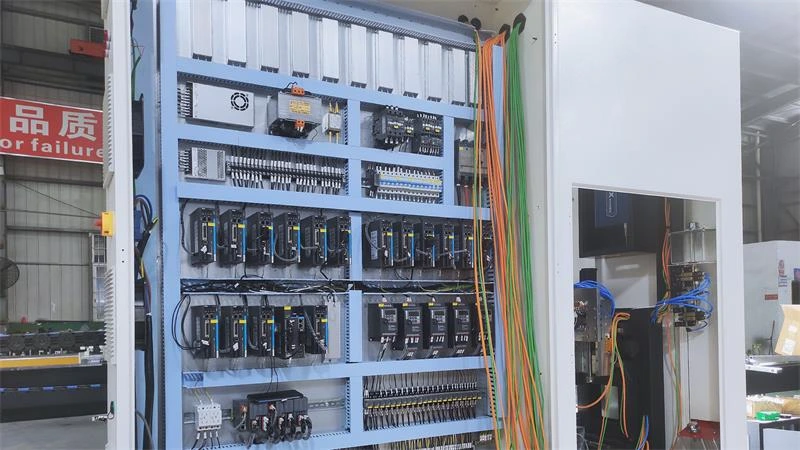
JH has a thorough quality management system encompasses every production phase, including design, development, manufacturing, testing, and delivery. This system guarantees that all processes are meticulously documented, monitored, and subject to ongoing enhancement to uphold consistency and dependability.
The production process is carefully monitored at every stage, encompassing material selection, precise machining, assembly, and final inspection. Through the use of standardized workflows and thorough evaluations, we guarantee that each piece of equipment adheres to rigorous quality standards.
JH uses state-of-the-art inspection equipment to perform multi-stage testing on all components and finished products. These tests include part calibration, assembly inspection, and final performance testing. We document and share inspection results with our clients to provide full transparency and confidence in our products.
How many years of industry experience do you have?
Over 30 years.
How many clients have you served?
We have served clients in over 270 countries, with more than 7,500 customers worldwide.
What if there’s a shortage of spare parts?
We include an extra set of spare parts with every machine to prevent shortages and simplify future part replacements for our customers.
How is your after-sales service?
We provide lifetime remote after-sales support for all our customers.
How do you ensure product quality?
We enforce strict quality control using advanced inspection equipment to verify the quality of every machine before it leaves the factory. The inspection results are documented and shared with customers for transparency.
contact us
If you have any needs or would like to receive exclusive offers, updates, and more information, please leave your contact details below, and we will get in touch with you promptly.